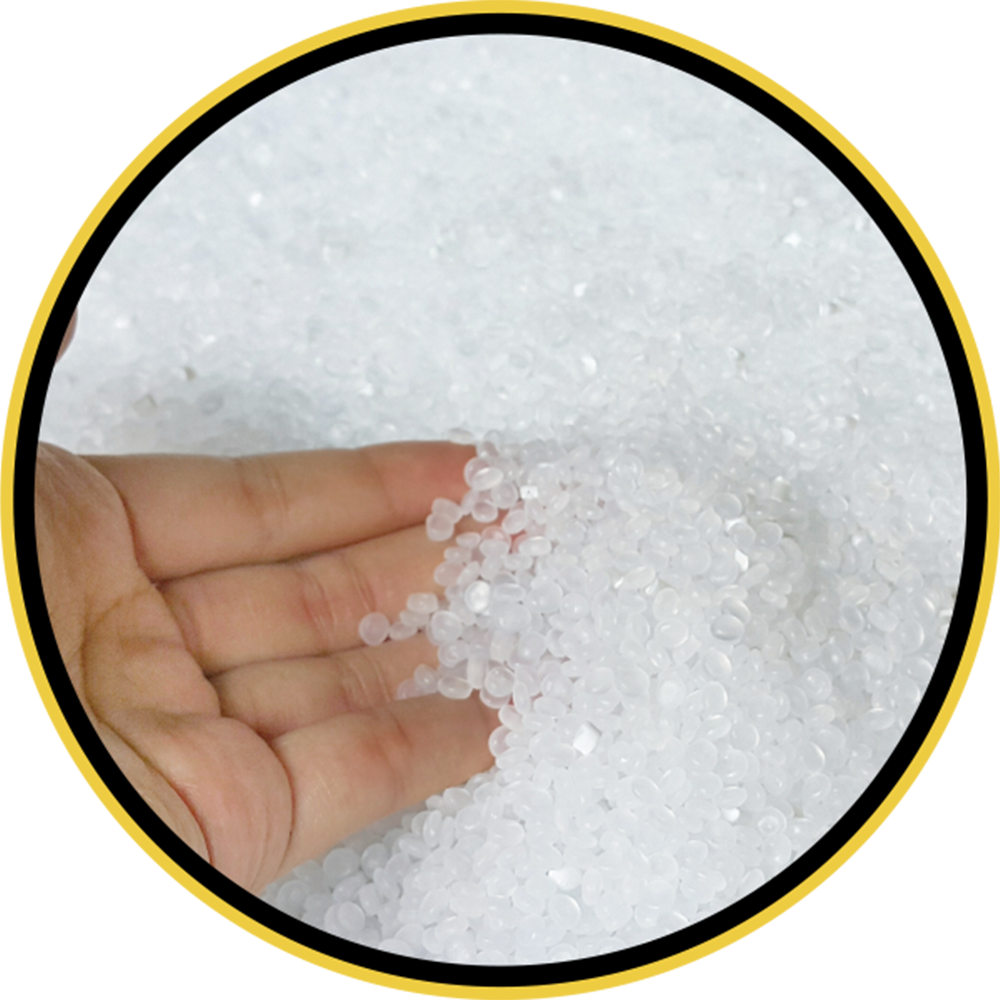
PP (Polypropylene)
Polypropylene is a synthetic, thermoplastic polymer made from the combination of propylene monomers and is used in a wide variety of applications. Polypropylene is the second-most widely produced commodity plastic. This material has a high strength-to-weight ratio, high melting point, and good chemical resistance properties. It doesn’t break down easily and can withstand daily wear and tear. Because of its unique properties, it is a very useful plastic in the commercial, industrial, and fashion industries.
PVC (Polyvinyl Chloride)
Polyvinyl Chloride is an economical, strong, and versatile thermoplastic material widely used in the construction industry to produce long-lasting buildings. It is the third most-produced synthetic plastic polymer with about 40 million tons produced each year. Polyvinyl Chloride can be used in varied applications. The rigid PVC is ideal in construction materials, doors, windows, bottles, non-food packaging, and more. The flexible PVC is used in plumbing products, electrical cable insulation, clothing, medical tubing, etc.
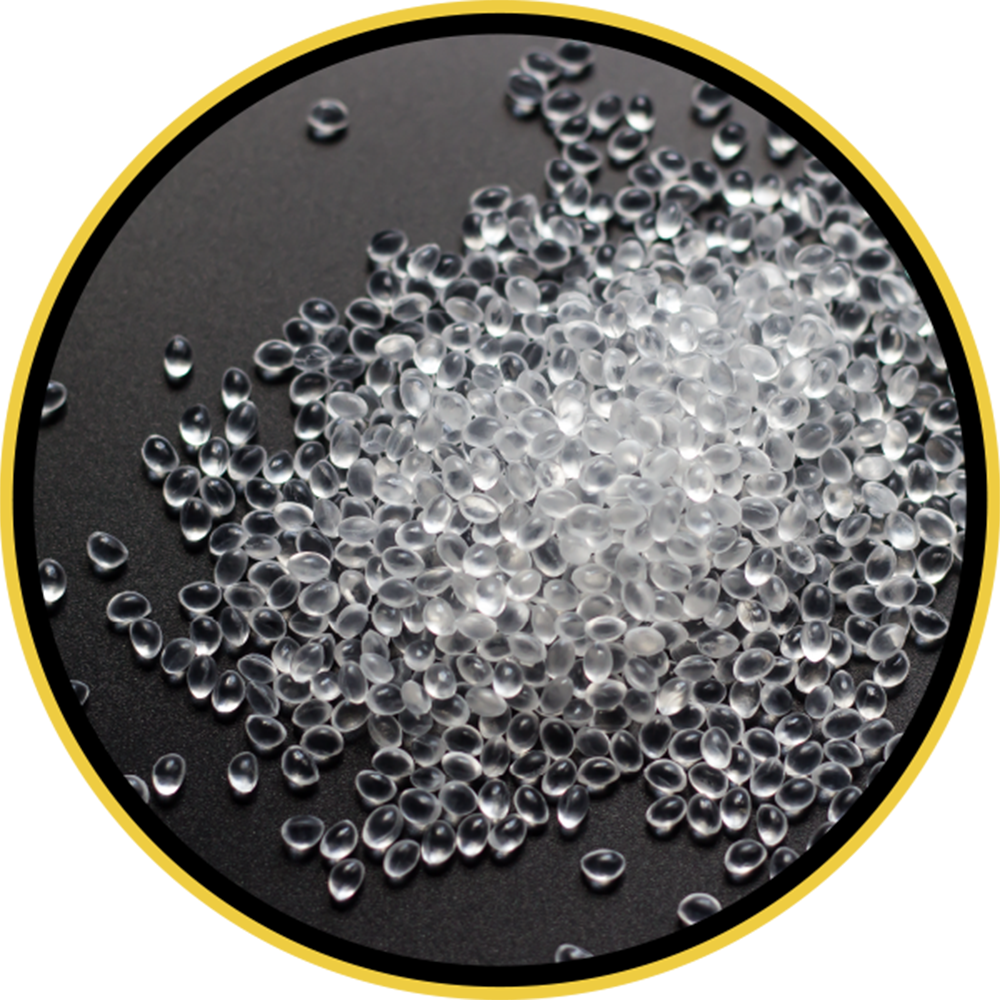
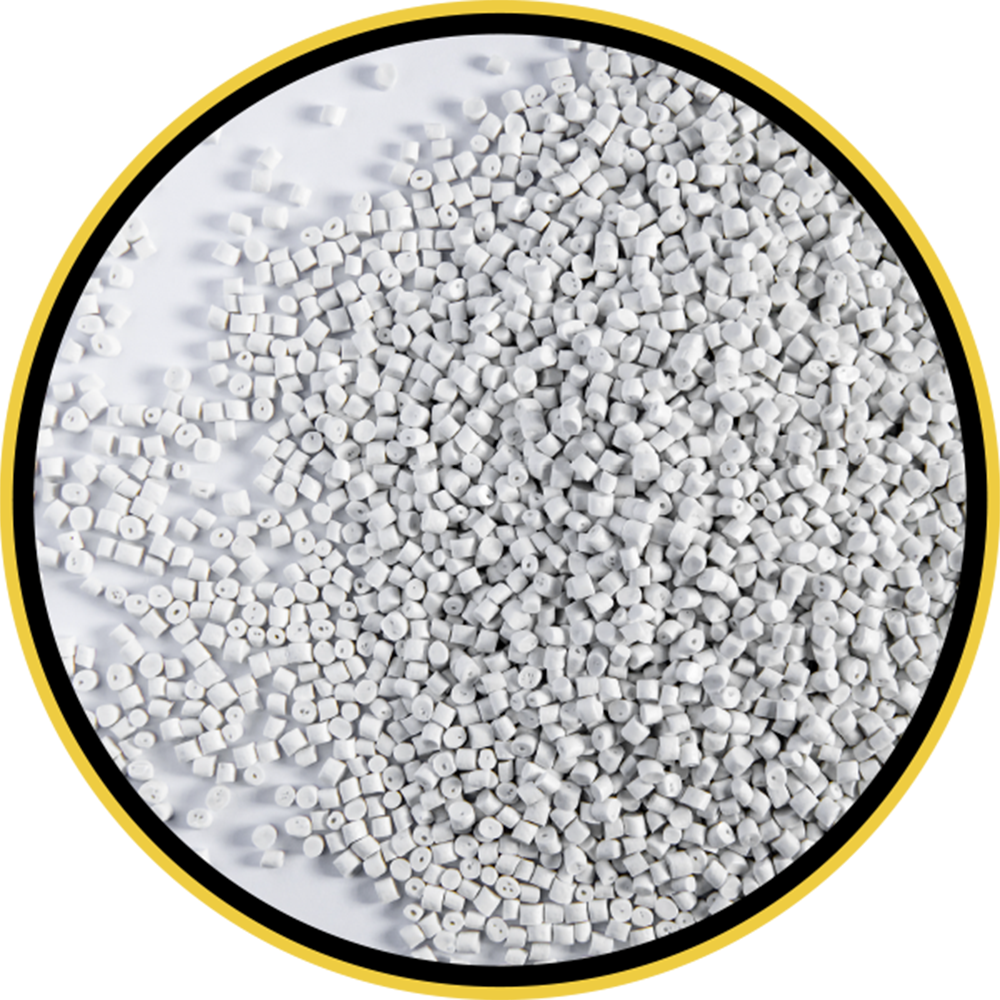
ABS (Acrylonitrile-Butadiene-Styrene)
Acrylonitrile-Butadiene-Styrene is made with the polymerization of styrene and acrylonitrile in the existence of polybutadiene. It is a common thermoplastic polymer that has countless applications. From appliance housings and automotive parts to pipe fittings and Lego toys. ABS is very sturdy and is an ideal choice if you need an inexpensive, durable, and stiff plastic that can withstand external impacts.
PE (Polyethylene)
Polyethylene is a type of thermoplastic polymer derived from ethylene. It is lightweight, strong, and with a variable crystalline structure. Depending on the particular type, it can be used in a vast range of applications. For example, Low-Density Polyethylene (LDPE) is generally used in plastic packaging such as plastic wrap and grocery bags. High-Density Polyethylene (HDPE) is widely used in constructions and Ultrahigh Molecular Weight Polyethylene (UHMW) has high-performance applications in things such as bulletproof vests.
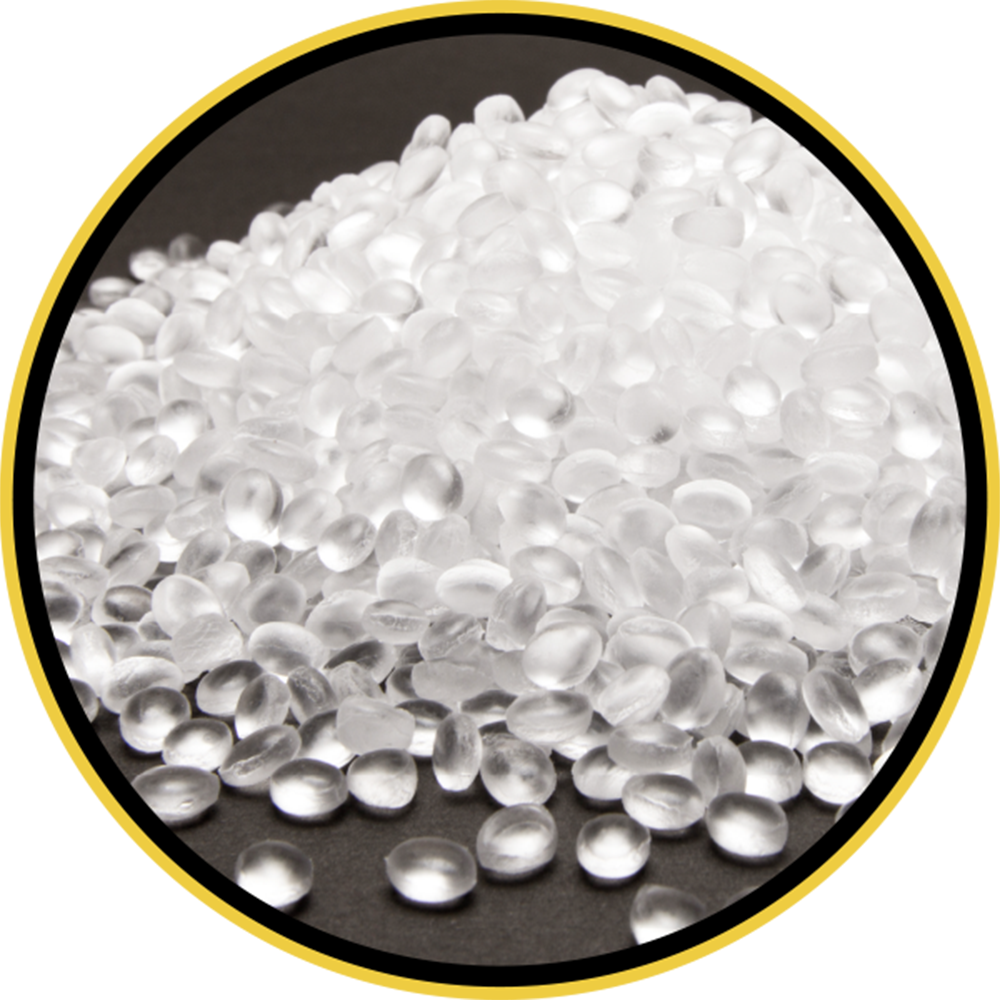
PRODUCING PLASTIC PARTS WITH INJECTION AND CAST MOLDING
There are two common manufacturing processes – injection molding and cast molding. Each of these processes is beneficial in manufacturing.
Injection Molding is the process of injecting plastic material into a mold under high pressure while in a liquid state to create the desired object. It is one of the most cost-efficient methods to make a product. This type of manufacturing process is simple and inexpensive, allowing the manufacturers to have a higher quality product, cut costs and price their products more competitively.
Cast Molding, on the other hand, is a process in which the liquid material is poured into a mold. This manufacturing process results in a durable high-quality product. It is often used for making and completing complex shapes and designs.
CUSTOM PRODUCTION, CATERED TO YOUR PRODUCT & VISION
We have been providing packaging solutions for over two decades and have been instrumental in assisting our customers to reach their goals. Each customer has their own needs and we always give these according to their personal preferences and demands.
At WBA Corporation, we are dedicated to providing our customers with premium quality products at remarkably affordable rates and delivered on short timelines.
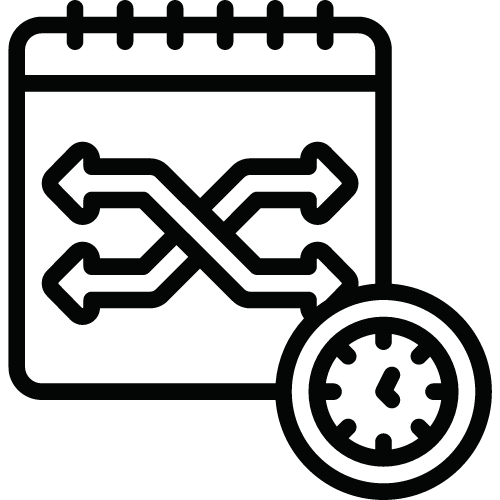
DESIGN FLEXIBILITY
For complex shapes, lightweight characteristics, and appealing designs.
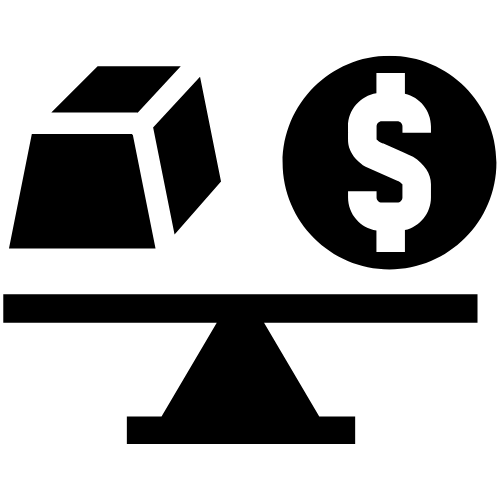
COST-EFFECTIVE
Spend less money without sacrificing your products’ quality or performance.
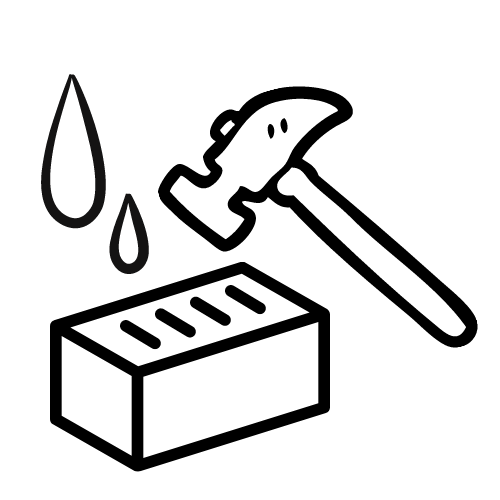
HIGH DURABILITY
Durable materials that resist chemical, physical, and environmental attacks.
GET IN TOUCH
Have an idea or a project, lets collaborate and build some awesome stuff